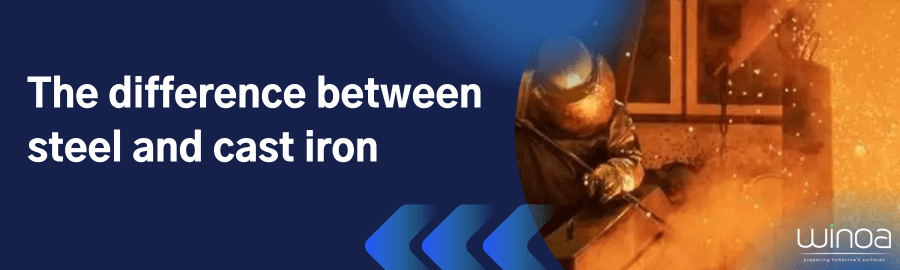
If you work in the blasting industry, you know that choosing the right material for your abrasive is crucial to achieving the desired result. Two of the most common materials used for making metal shot are steel and cast iron, but people are often unsure of the difference between the two. In this article, we will explore the differences between cast iron and steel and how these affect the choice of the right abrasive for your blasting process.
Cast iron is an iron alloy with a significant amount of carbon, usually between 2.1% and 4.3%: thanks to this feature, cast iron is an extremely hard material, ideal for applications requiring strong abrasion such as blasting cast iron parts, cleaning boiler pipes, removing resistant paint, and much more.
Steel is also an iron and carbon alloy, but with a lower carbon content than cast iron. Steel may also contain small percentages of other elements, such as chromium or nickel, to improve its mechanical properties. To eliminate the risk of corrosion when used in humid environments (such as, for example, in stainless steel grit Stelux) these percentages increase. Thanks to its corrosion resistance, wear resistance, and flexibility, steel is used in numerous applications, such as foundry, construction, automotive, shipyards, aerospace and many others.
Steel and cast iron grit are both widely used as abrasives for cleaning and preparing surfaces. However, they have some significant differences in terms of performance and properties.
In general, cast iron has a higher hardness but at the same time is more brittle and less ductile. This means that cast iron shot tends to break into larger pieces compared to steel shot. Cast iron has a higher specific weight than steel, which makes it more effective for removing heavy scale, rust, and casting residues. The greater inertia due to its weight can result in higher kinetic energy during impact on the surface. Cast iron grit can be easily produced as a byproduct of other cast iron manufacturing processes and can also be obtained by recycling waste, which can translate into a lower production cost.
Instead, the advantages of steel grit compared to cast iron grit can be summarized as follows:
1. Durability: steel shot is generally more durable than cast iron shot, which means it can be reused for more cycles. This reduces the cost of materials in the long run and makes the process more environmentally sustainable.
2. Elasticity: steel shot has greater elasticity than cast iron shot, allowing for better impact absorption and a lower probability of breakage. This can reduce dust generation and wear and tear on the equipment used in the blasting process.
3. Controlled Shape: steel shot is produced in a more uniform and regular shape than cast iron shot. This ensures greater homogeneity of the sandblasting process, resulting in a more uniform finish on the treated surface.
4. Lower incidence of contamination: steel shot has a lower probability of contaminating the treated surface with iron particles or other elements, unlike cast iron grit. This is especially important in applications where high cleanliness is required, such as aerospace or food processing.
So which material should you choose for your sandblasting shot? It depends on the specific needs of your work but in summary, steel shot compared to cast iron shot has the advantages listed above.
In any case, make sure you choose a reputable blasting media manufacturer who can guarantee you product quality and compliance with safety standards. With the correct abrasive, you can achieve excellent results and guarantee the best safety conditions in the workplace.