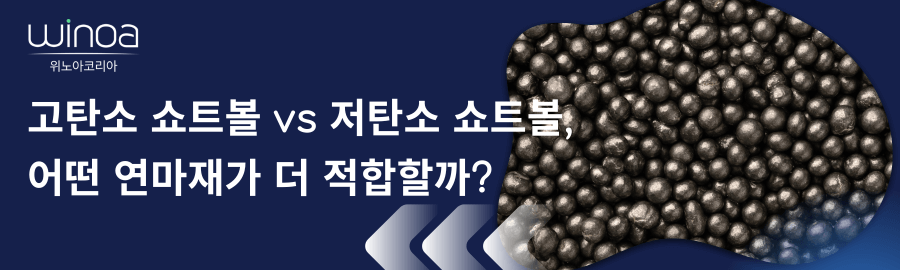
금속 표면 처리 공정 (쇼트 블라스트 공정)에서 사용하는 연마재(투사재)는 단순한 소모품이 아닌, 제품 품질, 작업 효율성에 큰 영향을 주는 요소 중 하나인데요. 특히 고탄소 쇼트볼과 저탄소 쇼트볼은 비슷한 듯 보여도, 실제로는 적용 방식과 목적이 전혀 다릅니다. 이번 포스팅에서는 두 제품의 특성과 현장에서 어떤 기준으로 선택해야 하는지 살펴보겠습니다.
고탄소 쇼트볼
– 다양한 조건의 작업에 유연하게 대응하고 싶다면
고탄소 쇼트볼은 경도 조절이 가능하고, 형태도 쇼트볼(구형) 또는 그리트(각형) 중 선택할 수 있어 다양한 쇼트 블라스팅 작업에 맞춰 활용할 수 있는 범용성이 뛰어난 연마재입니다.
예를 들어,
- 도장이나 용접 후에 남은 강한 스케일 제거가 필요할 때
- 표면에 깊은 부식이 생긴 철 구조물을 처리할 때
- 혹은 두꺼운 코팅층을 빠르게 벗겨내야 할 때
고탄소 쇼트볼은 강한 타격력으로 빠르고 강력하게 표면을 정리할 수 있는데요. 다만, 경도가 높은 만큼 설비 내부의 마모가 빠르게 진행될 수 있기 때문에, 기계 부품의 마모율과 유지보수 주기까지 함께 고려해 연마재를 선택하는 것이 중요합니다.
저탄소 쇼트볼
– 기계 보호가 중요하거나, 비용 효율이 중요한 현장에
저탄소 쇼트볼은 고탄소 대비 경도가 낮고, 파쇄가 잘 일어나지 않는 특성을 가지고 있어,
제품 표면을 손상시키지 않으면서도 부드럽게 처리해야 하는 작업에 적합합니다.
예를 들어,
- 알루미늄처럼 긁힘이나 눌림에 민감한 재질
- 정밀하게 가공된 주물 부품
- 외관 품질이 중요한 고급 부품 등
이런 제품은 형태나 표면 질감을 유지하면서도 불순물이나 산화물을 부드럽게 제거해야 하는데, 저탄소 쇼트볼은 이러한 목적에 딱 맞는 연마재입니다. 또한, 파쇄율이 낮고, 분진 발생이 적으며, 소모량이 적어 설비 유지관리 비용 절감 측면에서도 효과적입니다.
고탄소 vs 저탄소 쇼트볼 총정리
고탄소 쇼트볼과 저탄소 쇼트볼 중 선택 시에는 단가뿐 아니라,
[ 작업 목적 / 제품의 재질 특성 / 품질 기준 / 비용 효율성 / 작업 안정성 ] 등을 종합적으로 고려해 결정해야 합니다.
특히 코일 가공, 주물 산업, 알루미늄 가공 산업처럼 공정 특성과 작업 대상이 다양하게 바뀌는 산업군에서는, 두 제품 중 어느 것이 더 효율적일지 작업 조건에 맞는 제품을 유연하게 선택하는 것이 중요합니다.
아래 비교표를 참고해 귀사의 공정에 어떤 연마재가 더 적합한지 아래 표에서 체크해 보세요.
구분 | 고탄소 쇼트볼 | 저탄소 쇼트볼 |
적용 공정 | 스케일 제거, 녹 제거, 코팅 제거 | 정밀 주물, 알루미늄, 연질 소재 처리 |
표면 충격력 | 강함 (공격적인 블라스팅) | 부드러움 (기재 보호 중심) |
설비 마모도 | 상대적으로 높음 | 낮음 (설비 수명 연장에 유리함) |
소모량 | 비교적 많음 | 비교적 적음, 먼지 발생 적음 |
라인 유연성 | 경도/형태 조절 가능, 공정 다양성 높음 | 표준화된 반복 공정에 적합 |
추천 산업 | 조선, 철강 가공, 중장비 제조 | 주조, 알루미늄 부품, 자동차 부품 |
최적의 연마재 조합, 현장에서 찾아야 합니다.
쇼트 블라스트 작업은 현장의 설비 조건, 투사 압력, 라인 속도, 그리고 제품의 재질 특성 등 복합적인 변수들이 서로 얽혀 있기 때문에 실제로 적용해보지 않고는 결과를 예측하기가 어렵습니다.
예를 들어, "고탄소 쇼트볼을 선택했지만 설비가 그 강한 압력을 견디지 못해 예상보다 빠르게 마모가 일어나는 경우" 혹은 "저탄소 쇼트볼을 사용했는데 표면 처리 강도가 부족해 품질 불량으로 이어지는 사례"처럼, 다양한 변수를 고려하지 않은 채 연마재(투사재)를 선택한다면 제품의 품질 저하와 비용 증가로 이어질 수 있습니다.
이런 리스크를 줄이려면,
현장 조건에 맞춘 사전 테스트와 설비 진단을 포함한 전문가의 컨설팅이 필요합니다.
|
위노아코리아는 다양한 산업과 공정에 맞춘 전문 컨설팅을 통해
귀사의 공정 효율과 품질 향상을 목표로 전체 운영 전략까지 함께 설계합니다.
지금, 귀사의 현장에 꼭 맞는 연마재를 함께 진단해 보세요!